摘 要
本发明提供了一种稀土矿的冶炼分离方法。采用碳酸氢镁水溶液对硫酸焙烧矿浸出并中和除杂,固液分离得到含镁的硫酸稀土溶液;采用碳酸氢镁水溶液皂化P507或P204萃取转型或碳酸氢镁沉淀转型富集,得到高浓度的混合氯化稀土溶液,再经过萃取分离,碳酸氢镁水溶液沉淀回收稀土,得到多种稀土化合物产品。在上述工艺过程中产生的含硫酸镁废水,采用廉价的钙镁等碱性化合物进行碱转,并通入冶炼分离过程回收的CO2进行碳化提纯,得到碳酸氢镁水溶液,循环用于稀土浸出、转型、萃取分离和沉淀工序,实现镁和CO2的循环利用、氨氮和废水零排放,而且大幅度降低生产成本、提高稀土的回收率,实现稀土绿色环保、高效清洁生产。
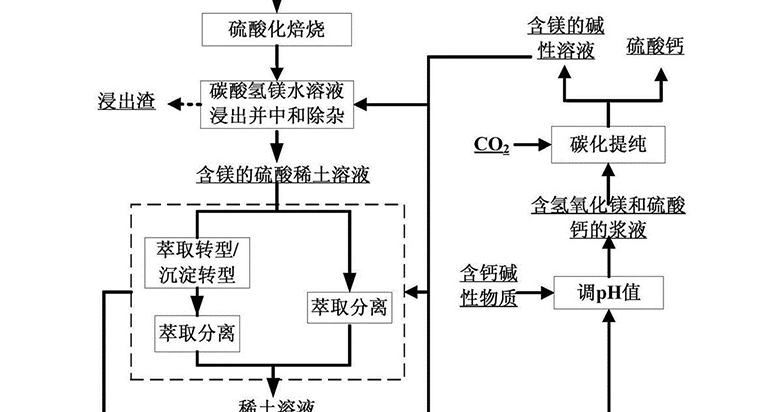
背景技术
目前,稀土的冶炼分离与提纯一般采用溶剂萃取法,但稀土冶炼工艺存在着酸碱用量大、成本高、废水排放量大等问题。如包头混合型稀土矿主要采用硫酸焙烧-水浸-氧化镁中和除杂-萃取转型或萃取分离工艺,得到的硫酸稀土溶液需要加入大量的固体氧化镁中和余酸并调节pH除杂,由于轻烧氧化镁中杂质含量高、固体反应速度慢,导致未反应的氧化镁及其杂质形成大量废渣;pH值变化滞后难以控制,导致稀土沉淀损失,且大量废渣吸附稀土离子,降低稀土回收率;在稀土萃取转型和分离过程产生大量含硫酸和硫酸镁的酸性废水,等均需要大量的碱中和处理,废水中含大量的钙离子,返回使用容易富集形成硫酸钙结晶,堵塞管道,或在萃取过程形成三相物,影响分相等,废水难以循环利用。
传统的稀土冶炼工艺中采用氨水或氢氧化钠对有机萃取剂进行皂化,将氢离子置换去除,然后与稀土离子进行交换萃取分离。然而在萃取过程中消耗大量的液氨或液碱,造成成本增加且产生大量的氨氮废水或高钠盐废水等。
为中和大量的酸性废水,传统的化学中和法加入石灰或电石渣等进行中和处理,产生大量硫酸钙、氟化钙或氢氧化镁等沉淀物,澄清处理后废水达标排放。该技术的消耗主要是石灰或电石渣等中和剂,但处理后的废水中钙离子、镁离子和硫酸根离子含量饱和。废水循环使用时,随着温度的变化在管道、输送泵或储槽上容易形成硫酸钙等结垢,严重影响废水的循环利用,对连续化生产造成了较大影响。此外,直接外排的废水含盐量高,将导致江河水质矿化度提高,也会给土壤、地表水以及地下水带来越来越严重的污染,危及生态环境。随着新的环保法颁布实施,解决高盐废水问题以及废水的近零排放将是最终目标。
在稀土冶炼废水的回收循环利用的研究和应用上,目前研究较多的是采用膜分离法、蒸发结晶法、汽提法和折点氯化法等。膜分离法是利用选择透过性分离水中的离子、分子或者微粒,处理效果较好,但易造成膜污染。蒸发结晶法是指含盐废水经蒸发浓缩,达到过饱和状态,使盐在废水中形成晶核,继而逐步生成晶状固体分离的方法,此方法适用于高盐废水的处理。汽提法是指让废水与水蒸汽直接接触,使废水中的挥发性物质按一定比例扩散到气相中去,从而达到从废水中分离污染物的目的,用于易挥发性污染物的处理。折点氯化法是将一定量的氯气或次氯酸钠加入到废水中使氨氮被氧化为N
2
而达到去除氨氮的目的。这些方法均具有运行费用较高,投资费用大的缺点,限制了其在工业上的应用。
因而,仍需要对现有的稀土冶炼分离方法进行改进,以简化生产工艺,提高稀土回收率,降低渣量排放,降低生产成本。